Typical Uses of Chemical Defoamer Across Various Industries
Typical Uses of Chemical Defoamer Across Various Industries
Blog Article
How a Chemical Defoamer Can Improve Efficiency in Your Procedures and Procedures
In today's competitive industrial landscape, functional performance is paramount, and the function of a chemical defoamer can not be ignored. By attending to foam-related difficulties that interfere with processes, defoamers not just promote smoother procedures yet also add to cost financial savings and enhanced product high quality. Their effect extends numerous industries, making them an important consideration for those seeking to maximize efficiency. However, understanding the particular benefits and applications of defoamers increases essential concerns regarding their choice and execution. What factors should you think about to maximize their efficiency in your procedures?
Recognizing Chemical Defoamers
Chemical defoamers play a vital function in different commercial procedures by efficiently preventing and lowering foam development. Lathering can lead to functional ineffectiveness, boosted production prices, and jeopardized product top quality. Defoamers are specialized chemical additives designed to interfere with the stability of foam bubbles, thus allowing smoother processing and boosted efficiency across numerous industries, consisting of food and drink, pharmaceuticals, and wastewater treatment.
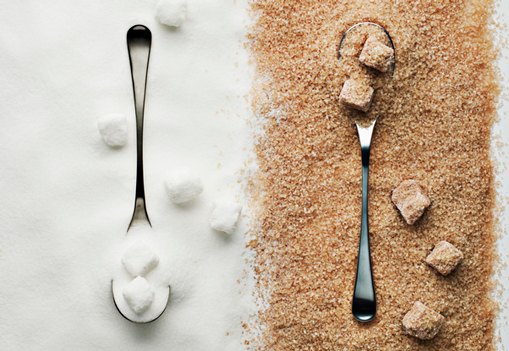
These representatives generally are composed of surfactants, oils, or polymeric compounds that reduced the surface tension of the liquid, promoting the collapse of foam. The system through which defoamers operate frequently includes the destabilization of foam structures, allowing for quicker drain of fluid and the release of entraped air. Different formulas are customized to particular applications, considering variables such as compatibility with the system, temperature, and the nature of the fluid being treated.
Comprehending the make-up and functionality of chemical defoamers is crucial for selecting the proper item for an offered application. By optimizing defoamer choice based on procedure requirements, industries can enhance operational efficiency, alleviate foam-related obstacles, and inevitably improve overall efficiency.
Advantages of Using Defoamers
Utilizing defoamers can substantially improve operational performance throughout various industries by successfully minimizing foam-related issues. The presence of foam can interrupt procedures, resulting in boosted downtime, lowered efficiency, and possible high quality deterioration in output. Defoamers assist battle these challenges by breaking down foam structures, thereby permitting smoother operations.
One of the primary benefits of using defoamers is the decrease of waste and rework. By decreasing foam formation, defoamers boost the uniformity of processes, making sure that products are utilized effectively. This not only reduces operational costs but also adds to sustainability initiatives by reducing source usage.
Furthermore, defoamers can enhance product quality. In manufacturing setups, too much foam can bring about incongruities in item features, affecting client complete satisfaction. By controlling foam levels, defoamers aid preserve the preferred physical residential properties of products.

Applications in Different Industries
The performance of defoamers expands across a variety of markets, where their application addresses particular foam-related difficulties intrinsic per field. In the food and beverage industry, defoamers are important for enhancing manufacturing processes, such as brewing and dairy processing, where extreme foam can impede circulation prices and minimize performance. By decreasing foam, these agents enhance product top quality and uniformity.
In the chemical manufacturing field, defoamers are utilized in processes like paint production and wastewater treatment. Below, they protect against foam development that can disrupt blending and separate stages, thus enhancing the general performance and efficiency of procedures.
In pharmaceuticals, defoamers play a crucial duty in the solution of fluid medicines, making sure appropriate dosage and stability by controlling foam throughout blending and storage space. (Chemical Defoamer)
In addition, in the farming market, defoamers are utilized in chemical formulas to boost application effectiveness and minimize waste.
Choosing the Right Defoamer
Selecting the appropriate defoamer is vital for achieving optimum performance in different applications. The choice process must begin with a thorough understanding of the certain concerns available, including the kind of foam existing, the processing problems, and the chemical compatibility with various other formulation components.
Defoamers are created from a range of materials, consisting of silicone, mineral oils, and fats. Identifying the appropriate structure is vital, as different products exhibit differing efficiency in varied atmospheres. Silicone-based defoamers are typically preferred in high-temperature applications due to their stability, while natural defoamers may be extra appropriate for water-based systems.
Additionally, think about the defoamer's influence Your Domain Name on the last product. Some solutions can alter the practical or visual properties, making it vital to select helpful resources a defoamer that satisfies product requirements without endangering quality.
Checking is another vital action in choosing a defoamer. Small trials can supply valuable understandings right into the defoamer's performance, enabling for changes before full-blown execution. By carefully examining these variables, businesses can improve performance and ensure that the defoamer efficiently satisfies their functional needs.
Ideal Practices for Implementation
Carrying out a defoamer effectively needs cautious preparation and adherence to finest techniques to maximize its effectiveness. Initially, conduct a thorough assessment of the specific application and foam qualities. Comprehending the type and resource of foam will certainly lead the selection of the most ideal defoamer formula.
Following, develop the ideal dose (Chemical Defoamer). Start with a small-scale test to determine the minimum effective concentration, as excessive usage can bring about adverse effects on item top quality or functional efficiency
Monitoring and adjusting the application method is essential; guarantee that the defoamer is introduced at the a fantastic read right factor at the same time for optimal effect, such as during blending or instantly after foam development.

Additionally, preserve clear interaction with all relevant workers to make certain constant application practices and to share insights on efficiency end results.
Conclusion
In verdict, the utilization of chemical defoamers plays a critical function in boosting operational effectiveness across varied sectors. By effectively destabilizing foam, these agents assist in quicker water drainage and air release, consequently decreasing disruptions and decreasing costs. The calculated application of defoamers not just boosts throughput yet additionally ensures consistent product high quality and resource optimization. Eventually, the consolidation of defoamers right into industrial procedures promotes integrity and contributes to overall performance enhancement.

In the food and beverage market, defoamers are crucial for enhancing manufacturing procedures, such as brewing and dairy products handling, where excessive foam can impede circulation prices and reduce effectiveness. Silicone-based defoamers are usually favored in high-temperature applications due to their stability, while organic defoamers might be extra suitable for water-based systems.
Report this page